# Commercial Kitchen Compliance for Medicinal Mushroom Product Manufacturing
The Legal Backbone of Medicinal Mushroom Manufacturing
Compliance in a commercial kitchen setting is essential for medicinal mushroom manufacturers to meet federal and state health codes. This involves understanding and adhering to:
– FDA regulations for dietary supplements and food products
– USDA oversight for organic certification
– Local health department inspections and permits
– GMP (Good Manufacturing Practices) compliance frameworks
– Certification of Occupancy to legally operate out of a commercial facility
– Food handler certifications for staff involved in production
Each of these elements ensures that medicinal mushroom products are not just safe, but also legally cleared to be distributed and sold to the public.
Medical Research Reinforces the Importance of a Sterile Production Environment
Compliance matters not just from a legal standpoint but also from a medical safety perspective. Multiple studies highlight the therapeutic potential of these fungi — but only when products are crafted under rigorously clean and standardized conditions.
A 2020 study in Nutrients illustrates how lion’s mane (Hericium erinaceus) supplements helped improve cognitive performance in older adults: [Read Study](https://www.mdpi.com/2072-6643/12/10/3028)
A 2016 review in Oncotarget reveals how reishi (Ganoderma lucidum) boosts immune responses and may support anticancer efforts through enhanced cytokine and NK cell activity: [Read Study](https://www.ncbi.nlm.nih.gov/pmc/articles/PMC5600715/)
On the other hand, a 2018 study in Frontiers in Microbiology warns of fungal and bacterial contamination risks with poorly handled mushrooms, underlining why sterile environments and proper storage are non-negotiable: [Read Study](https://www.frontiersin.org/articles/10.3389/fmicb.2018.02909/full)
To maintain the therapeutic integrity of mushroom-based products, every step — from drying and grinding to encapsulation and bottling — must occur in carefully sanitized and temperature-controlled facilities.
Understanding the Role of Lab Testing and Ingredient Sourcing
Medicinal mushrooms are bioaccumulators, meaning they absorb and store substances from their environment — including toxins like heavy metals. That’s why testing is vital.
Heavy Metal Screening: Every product batch must be lab-tested for compliance with allowable limits for arsenic, cadmium, lead, and mercury.
Dosage Consistency: Active ingredients such as beta-glucans, hericenones, polysaccharides, or psilocybin (in licensed states) must be consistent across batches. This ensures that consumers receive effective, reliable dosages.
Sourcing: Ingredients should be certified organic when possible, and all suppliers must provide detailed Certificates of Analysis (COAs). Manufacturers should maintain strict traceability logs as part of their quality management systems.
Psilocybin-Specific Compliance in Legal Markets
In jurisdictions like Oregon where licensed therapeutic use of psilocybin is allowed, the compliance bar is even higher. According to the Oregon Psilocybin Services division ([OHA link](https://www.oregon.gov/oha/ph/preventionwellness/pages/psilocybin.aspx)), manufacturers must meet exceptional cleanliness and regulatory thresholds.
Key requirements for psilocybin product production include:
– Operation inside state-approved and licensed facilities
– Cleanroom environments for contamination control
– Meticulous recordkeeping and inventory tracking
– Environmental monitoring to prevent microbial, mold, or endotoxin exposure
These measures are validated by clinical trials like the 2021 JAMA Psychiatry study, which demonstrated that regulated psilocybin therapy significantly reduced symptoms in patients with major depressive disorder. [Read Study](https://jamanetwork.com/journals/jamapsychiatry/fullarticle/2772630)
The high therapeutic potential of psilocybin and the legal sensitivity of its production demand unwavering compliance and attention to quality.
Conclusion: Compliance Is the Gateway to Quality, Trust, and Growth
As wellness brands expand into the thriving world of medicinal and functional mushrooms, commercial kitchen compliance becomes both a regulatory obligation and a critical marker of quality assurance. From proper sanitization and documentation to GMP adherence and lab testing, every step of the manufacturing process must align with food safety standards and maintain therapeutic efficacy.
By integrating scientific research with sound manufacturing processes, businesses can build loyal customer bases, prevent regulatory setbacks, and solidify their place in a highly competitive yet rewarding market. In the end, compliance is not merely red tape — it’s the gateway to offering trustworthy, life-enhancing mushroom remedies.
References
1. Nutrients – Hericium erinaceus and Cognitive Decline: [https://www.mdpi.com/2072-6643/12/10/3028](https://www.mdpi.com/2072-6643/12/10/3028)
2. Oncotarget – Ganoderma lucidum and Cancer: [https://www.ncbi.nlm.nih.gov/pmc/articles/PMC5600715/](https://www.ncbi.nlm.nih.gov/pmc/articles/PMC5600715/)
3. Frontiers in Microbiology – Microbial Contamination in Mushrooms: [https://www.frontiersin.org/articles/10.3389/fmicb.2018.02909/full](https://www.frontiersin.org/articles/10.3389/fmicb.2018.02909/full)
4. JAMA Psychiatry – Psilocybin-Assisted Therapy for Depression: [https://jamanetwork.com/journals/jamapsychiatry/fullarticle/2772630](https://jamanetwork.com/journals/jamapsychiatry/fullarticle/2772630)
5. Oregon Psilocybin Services: [https://www.oregon.gov/oha/ph/preventionwellness/pages/psilocybin.aspx](https://www.oregon.gov/oha/ph/preventionwellness/pages/psilocybin.aspx)
Summary:
As the medicinal mushroom industry continues to grow, manufacturers must ensure strict compliance with commercial kitchen regulations to meet safety and quality standards. This includes adhering to FDA, USDA, and local health department guidelines, as well as implementing good manufacturing practices (GMP) and proper ingredient sourcing and testing protocols. For psilocybin-containing products in legal markets, the compliance bar is even higher, requiring licensed facilities, cleanroom environments, and meticulous recordkeeping. By prioritizing compliance, businesses can build trust, prevent regulatory issues, and deliver effective, therapeutic mushroom remedies to consumers.
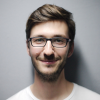
Dominic E. is a passionate filmmaker navigating the exciting intersection of art and science. By day, he delves into the complexities of the human body as a full-time medical writer, meticulously translating intricate medical concepts into accessible and engaging narratives. By night, he explores the boundless realm of cinematic storytelling, crafting narratives that evoke emotion and challenge perspectives. Film Student and Full-time Medical Writer for ContentVendor.com